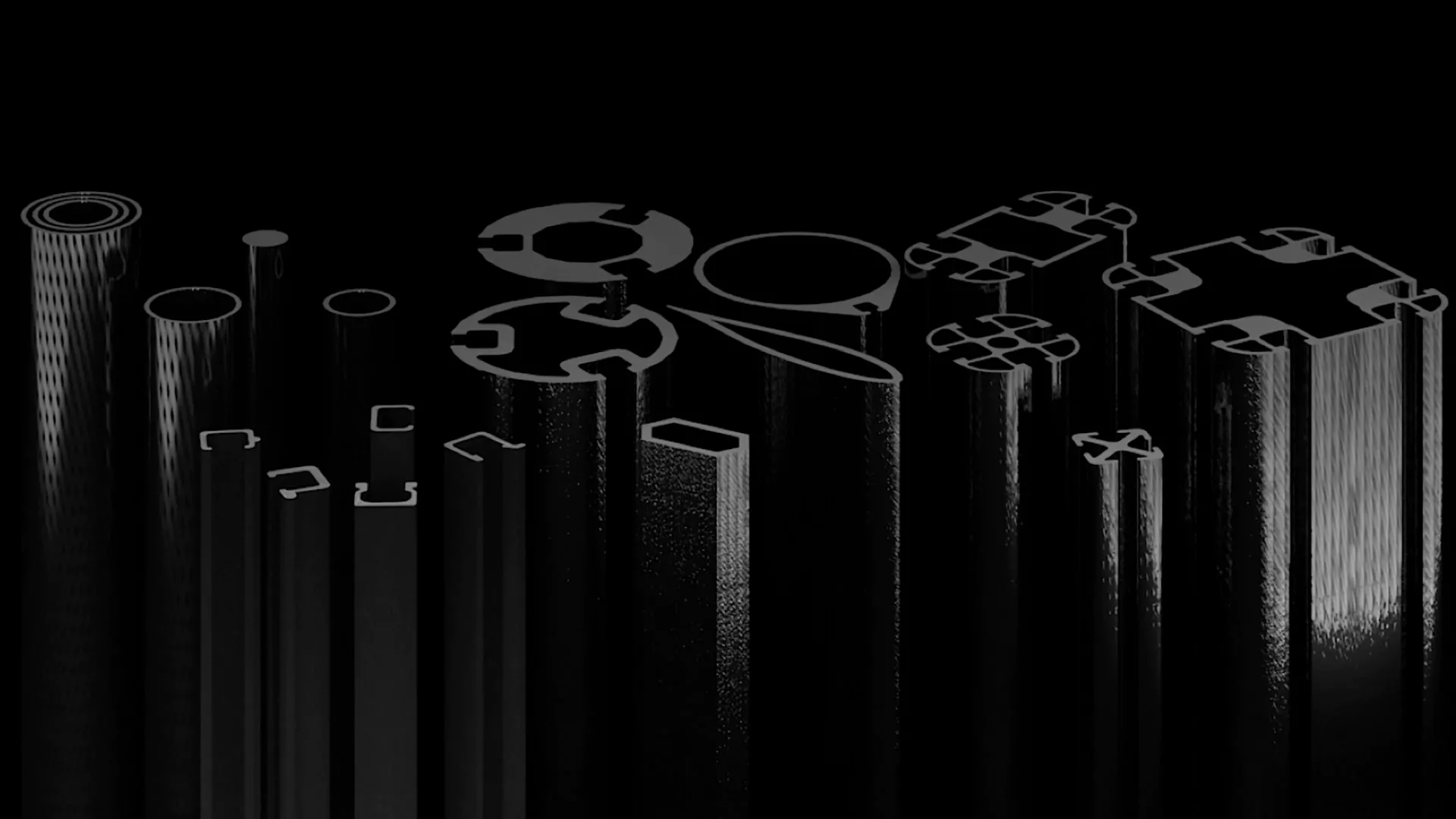
Pultrusion and pullwinding are the two technologies at the heart of our manufacturing process. These technologies are supported by R&D activities that include mechanical testing and various lab analyses in order to provide continuous improvement in product properties.
These methods combined with the properties of carbon fibers are the only viable options for reproducible manufacturing of cost-effective, high performance composite profiles at an industrial scale.
Pultrusion
Pultrusion is a continuous production technology with the unique capability to align the fibers along the longitudinal axis of the profile. . The aligned fibers are first impregnated with the resin and afterwards pulled through a heated die where the curing process takes place and the shape of the profile is defined. The cured profile is continuously pulled from the die to the cutting station, where it is cut to a determined length.
Mechanical properties of the composite material are mainly governed by the fiber properties, while its chemical and thermal properties are mainly controlled by the composition of the resin matrix. Outstanding tensile and bending resistance can be achieved through high fiber volume content, that with pultrusion can reach 70 %v .
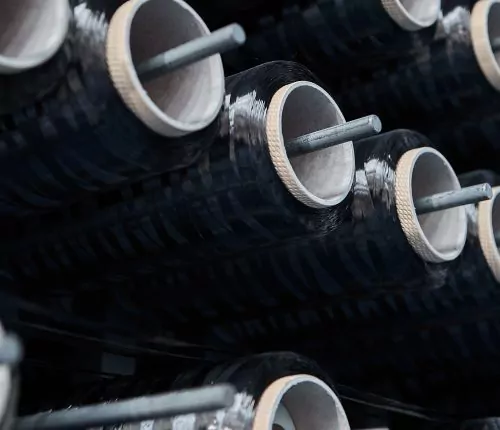
Pullwinding
Pullwinding is a form of pultrusion in which fibers are configured at different angles. The overall mechanical properties can be improved: better torsional resistance is obtained thanks to diagonally aligned fibers without compromising the tensile and bending properties of the profile.
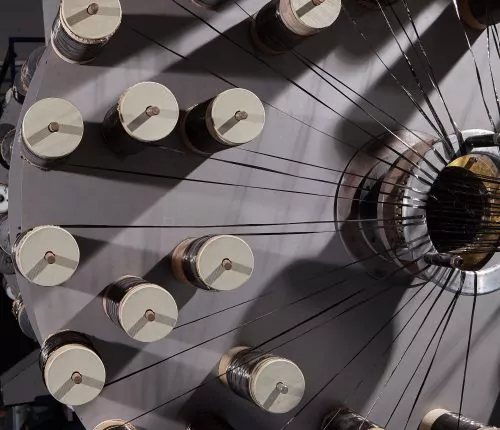
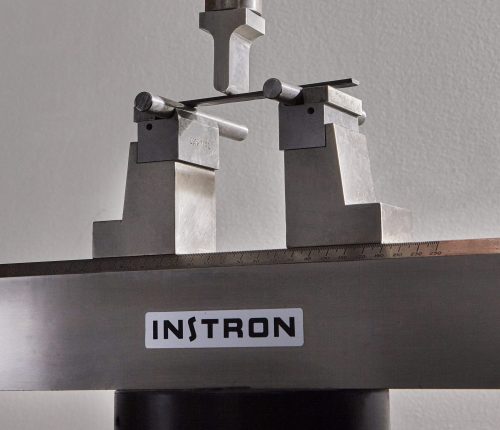
Research and Development
Research and development is the driving force of K-Composites, as innovative and competitive solutions can only come from continuous R&D activities. By introducing innovative raw materials and optimising the production process, the dedicated R&D team can deliver more performing, efficient and sustainable product solutions to our customers.
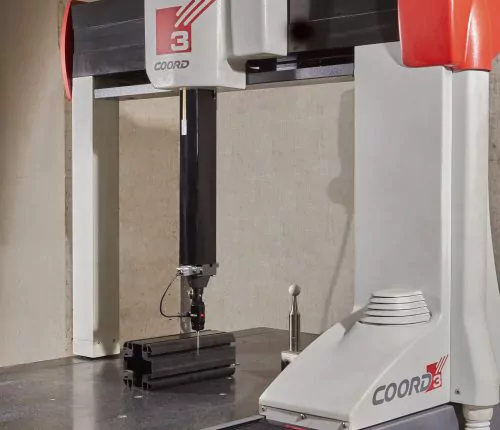
Testing
Whether it is for prototyping or R&D purposes, or just a quality inspection of standard production; various tests are carried out of different nature from destructive testing to dimensional control, DMA and DSC for physico-chemical properties determination, such as Tg or residual heat of reaction.
These tests provide key information to assess the performance of each product.
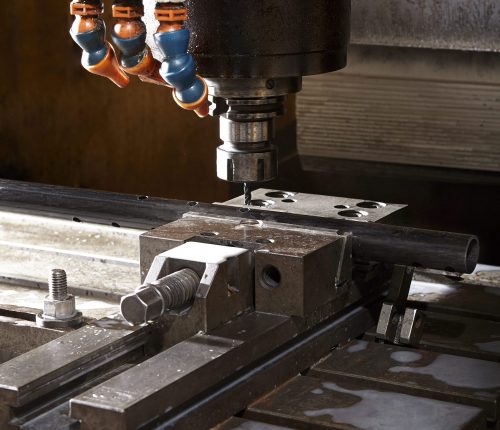
Post Production Process
Profiles from the pultrusion or pullwinding lines are already cut to required length. Yet, they can require further processing or treatments. Precision machining, surface treatments, post-curing, gluing are some of the processes and treatments that can be applied for assembly purposes or to improve the physico-chemical properties. These operations are executed by expert technicians.
Get to know more about the fields of application of our solutions and their unmatched advantages.